
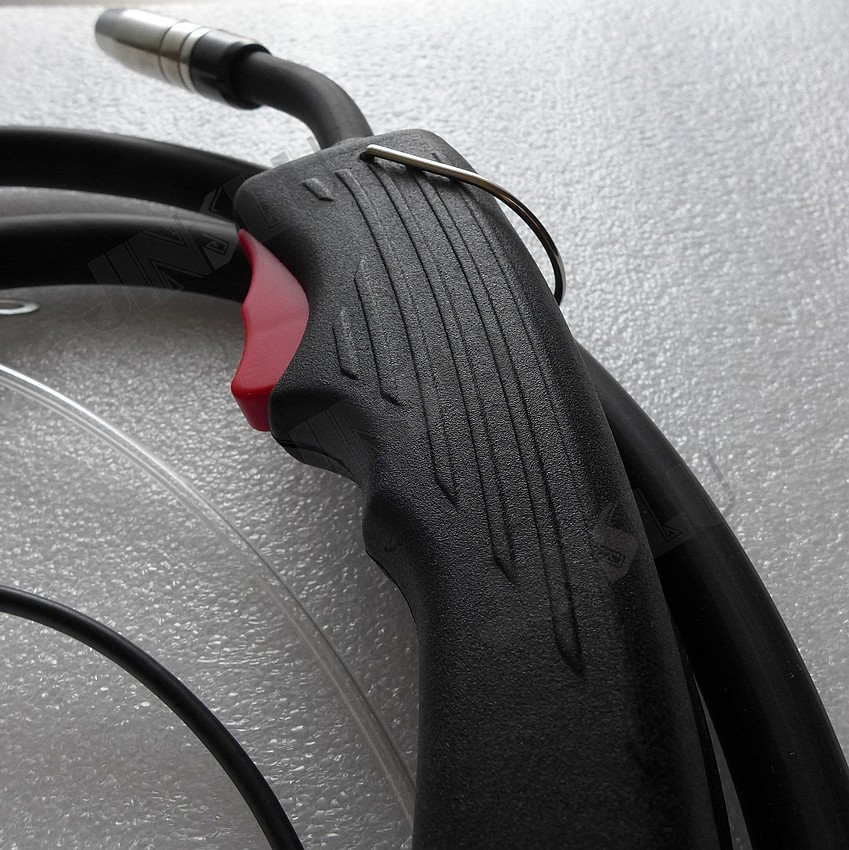
- WHAT IS A REPLACEMENT FOR CEBORA 130 MIG WELDER FULL SIZE
- WHAT IS A REPLACEMENT FOR CEBORA 130 MIG WELDER DRIVER
- WHAT IS A REPLACEMENT FOR CEBORA 130 MIG WELDER PROFESSIONAL
It also prevents 10Kgs or so of wire going rusty when the welder sits for a while.Īlso have a very close look at the drive rollers, but the liner sounds like the issue. In the past we have changed to a smaller wire spool, say 1 or 2 kgs, Don't know why it helps, but it seems to. The welding current is introduced at the tip, not through the liner. You can try a teflon liner, you're right,normally used with aluminium wire. **LINK**Įdit - it sounds as though I'm dismissing the replies you get here! Of course, I'm not, but you might get someone over there that has the same make of welder, liner and torch that you have and might be familiar with your particular problem. You might try asking on the mig welding forum. You might have an oversize wire - have you measured it? Have you checked the feed roller is correct / matched to wire diameter? How easily does it run with the tip removed? Get back to me? where do you reside?
WHAT IS A REPLACEMENT FOR CEBORA 130 MIG WELDER DRIVER
The charge is applied either at the roller driver or as it enters the torch 'hose'. Its normal for the wire to get tight around the swan neck. Sounds like something is out of alignment. 8 it would pass through the liner but not the tip?įirst things first, take a photo of your wire feed to include reel through roller and post it for apraisal. Have you checked that the new reel of wire does not have any rust on it ? Surely not the liner.as when using ally wire then u use a plastic liner (I think)? Where exactly does the weld wire get the current for welding.is it the copper nipple on the end ? Is there a new Teflon type liner to replace the spring type.?.if so what results. Never had a problem quite like this.which at least the grey cells can remember. This machine has only been used for mild steel welding since new.Īlso, the machine is stored and used in a warm room, kept constantly at 22C I've used mig's since they first came out.this machine is a quality unit and like me semi retired but "still working".

Now taken the new torch to bits, when feeding the fresh wire thru no problems but screw back on the bent part (head of the torch) the wire get's very very slow.remove the bent part, at the same feed setting, all OK. Having installed the new torch, the wire gets slowed down enough for the driving wheel to spin.tighten the tension screw and the wire ends up in a knot.
WHAT IS A REPLACEMENT FOR CEBORA 130 MIG WELDER PROFESSIONAL
the torch is a professional Binzal type, 4m long.still the same problem. The wire spool is new (15kgs) and have changed the liner with a brand new one, which is a close wound metal spring.still jamming.have now bought a quality new torch and cable complete (£100). Also the gas valve is in the handle and switches before the electrical suply, therefore much better control of gas.Problem is the mig wire (0.6 mild steel) keeps jamming in the cable / tube. The MIN/MAX & 1/2 settings would be much better for me if there were 6 levels instead! I really prefer it*, but wish it had more fine-tuning between settings. However, when running mine on 0.6mm wire & 0.6mm tip, I struggled to get anything close to a run and the wire was perpetually welded into the tip whenever it stopped.Īfter 18years & a lot of projects with the SIP I got myself a Clarke 130 tubo instead. Re-feeding the wire is another way to reduce the life of a torch liner!
WHAT IS A REPLACEMENT FOR CEBORA 130 MIG WELDER FULL SIZE
I used the full size wire spools to avoid needing to re-feed the wire (definately worth it if you have a lot to do). The roughened surface was probably a reason for needing regular torch liner changes. The wire surface is roughed up by the drive wheel which may help keep the tip bore cleaner. It has a couple of limitations, but as the roller drive for 0.8 is serrated and the wire is stronger, it can push the wire harder (less likely to stick in the tip). I replaced the full torch/cable assy twice and lots of torch liners as well.įor these, the 0.8mm wire together with a 1.00mm tip is a common preffered 'solution'.

I used a SIP migmate 130 tubo and recognise all the well-discussed issues you'll find on that welding forum.
